Precision Injection: Revolutionizing Metal Fabrication
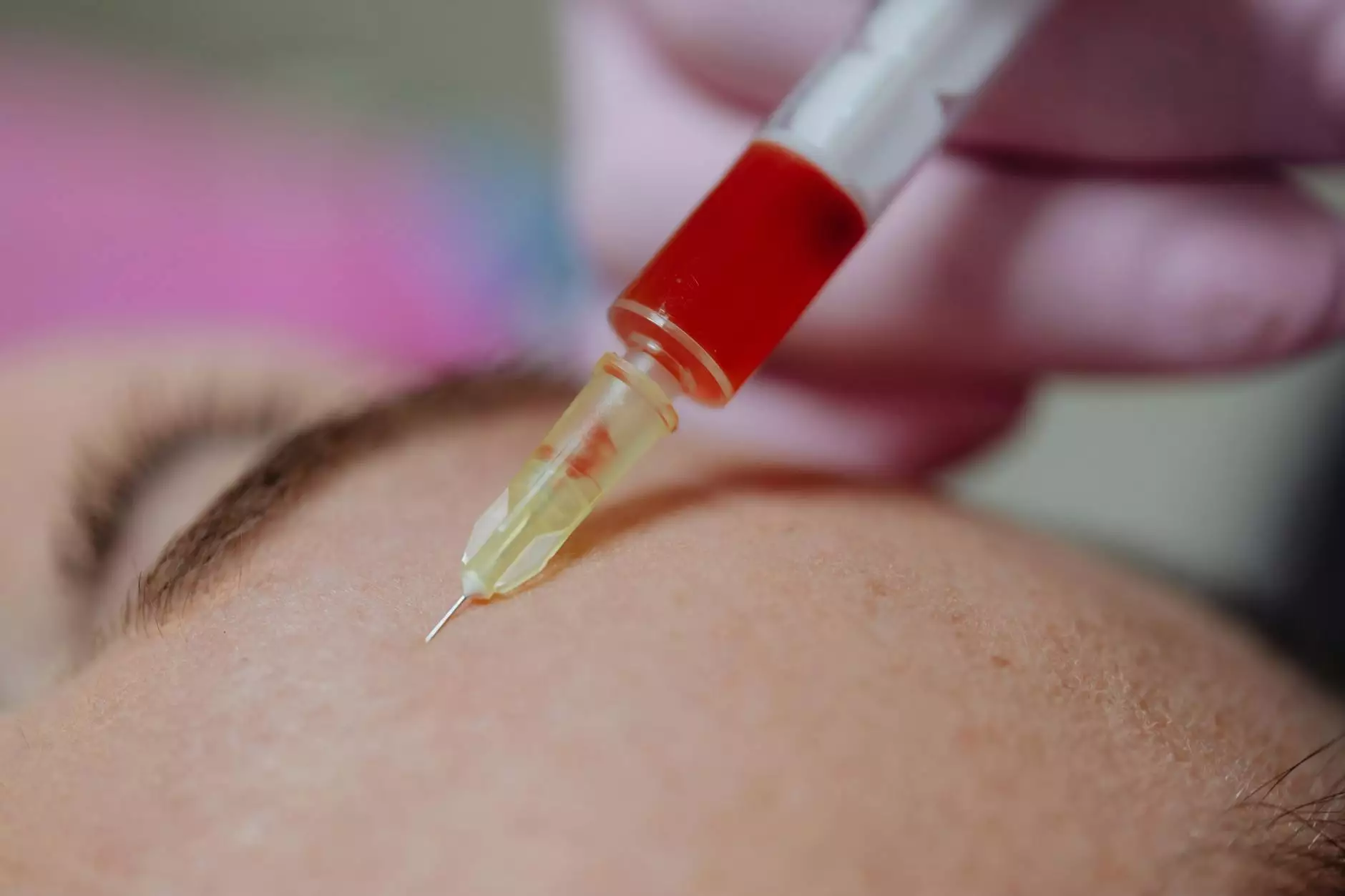
Precision injection is not just a buzzword; it represents a pivotal shift in the world of metal fabrication. This article will delve deep into the complexities of precision injection, its numerous benefits, and how companies like Deep Mould are leading the way in this innovative field. The demand for high-quality metal parts continues to rise, and precision injection is ensuring that manufacturers meet these challenges head-on.
The Fundamentals of Precision Injection
At its core, precision injection involves injecting molten material into a precisely engineered mold. This technique allows for the creation of complex shapes and detailed designs that would be virtually impossible to achieve through traditional metalworking methods. The process can be broadly outlined in several stages:
- Material Selection: Choosing the right alloy or material is crucial in achieving desired properties.
- Mold Design: Accurate design is essential for ensuring that the final product meets specifications.
- Injection Process: The molten material is injected into the mold under controlled conditions.
- Cooling and Solidification: Controlled cooling helps minimize defects and ensures dimensional accuracy.
- Finishing Processes: Post-process refinements, such as machining, surface treatment, or plating, enhance the final product.
Benefits of Precision Injection in Metal Fabrication
The advantages of adopting precision injection methods in metal fabrication are extensive. Here are just a few key benefits:
- High Tolerance Levels: Precision injection can achieve extremely tight tolerances, ensuring that parts fit together seamlessly.
- Enhanced Material Utilization: The process minimizes waste, making it more environmentally friendly and cost-effective.
- Complex Geometries: Designers can create intricate shapes and features that enhance product functionality.
- Improved Production Speed: The efficiency of the injection process reduces cycle times and increases output.
- Consistent Quality: With automated processes, manufacturers can achieve uniform quality across large production runs.
Precision Injection vs. Traditional Metal Fabrication Methods
When comparing precision injection to traditional metal fabrication techniques such as welding, casting, or machining, several distinct differences emerge:
1. Cost Efficiency
While initial setup costs for precision injection might be higher due to mold design and fabrication, the overall cost per unit can be lower than traditional methods for large runs. This is due to reduced material waste and faster production cycles.
2. Design Freedom
Precision injection enables manufacturers to explore innovative design possibilities, which can lead to new product development and market competitiveness. Traditional methods are often constrained by design limitations.
3. Scalability
With precision injection, scaling up production is seamless. Once the mold is created, additional units can be produced quickly and with minimal additional costs, which is often not the case with traditional methods that require more manual intervention.
Applications of Precision Injection in Modern Manufacturing
The versatility of precision injection makes it suitable for a wide variety of applications. Here are some of the industries benefiting from this advanced fabrication technology:
1. Automotive Industry
In the automotive sector, precision injection is utilized to create intricate components such as engine parts, transmission housings, and structural elements. These components need to meet stringent safety and performance standards, making precision manufacturing essential.
2. Aerospace
The aerospace industry demands incredibly precise parts that withstand high stress and extreme conditions. Precision injection allows for the creation of complex components that are both lightweight and strong, contributing to overall aircraft efficiency.
3. Consumer Electronics
The rapid evolution of technology requires consumer electronics to be not only functional but also aesthetically pleasing. Precision injection supports the intricate designs of smartphones, tablets, and laptops while maintaining high durability standards.
4. Medical Devices
In the medical field, precision is non-negotiable. From surgical instruments to implantable devices, precision injection is critical in achieving the accuracy and reliability required in medical applications.
The Role of Deep Mould in Precision Injection
As industry leaders, Deep Mould leverages state-of-the-art technology and expertise in precision injection to deliver unparalleled quality to its clients. Our commitment to excellence ensures:
- Advanced Technology: We utilize cutting-edge machinery and software to enhance precision and efficiency in our processes.
- Expert Team: Our skilled engineers and technicians possess deep expertise in metal fabrication and mold design.
- Customer-Centric Approach: We collaborate closely with our clients to tailor solutions that meet their specific needs and timelines.
- Quality Assurance: Rigorous testing and quality control protocols ensure that every part produced meets the highest standards.
Future Trends in Precision Injection
The field of precision injection is poised for continued growth, and several trends are set to shape its future:
1. Sustainability Practices
As environmental concerns grow, the industry is focusing more on sustainable practices, including energy-efficient processes and recyclable materials.
2. Automation and Robotics
Increased automation in precision injection will lead to improved efficiency, reduced human error, and lower labor costs.
3. Material Innovation
Research into new materials that can withstand higher temperatures and pressures will expand the applications of precision injection.
4. Industry 4.0 Integration
The rise of the Internet of Things (IoT) in manufacturing will bring smart factories where precision injection systems communicate and optimize processes in real-time.
Conclusion
In summary, precision injection is revolutionizing the landscape of metal fabrication by enabling rapid production of complex, high-quality parts. Companies like Deep Mould are at the forefront of this transformation, utilizing advanced technologies to support diverse industries. As we look towards the future, embracing sustainability, and integrating cutting-edge technologies will be essential in meeting the evolving demands of global markets. By understanding and leveraging the benefits of precision injection, manufacturers can position themselves for success in an increasingly competitive world.
For more insights and professional services in precision injection and metal fabrication, visit Deep Mould today!