Understanding Phosphating Plants: A Comprehensive Guide for the Automotive Industry
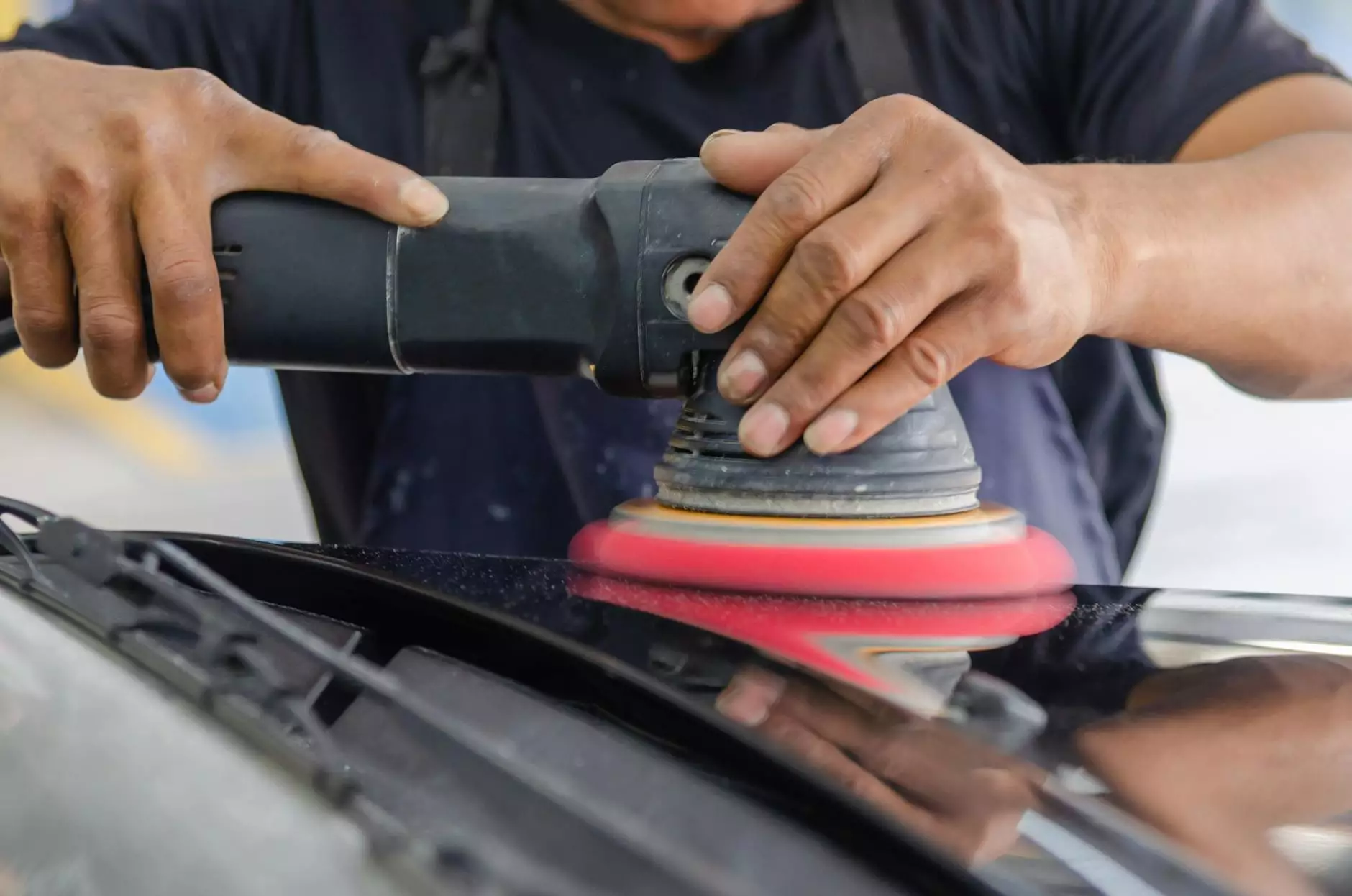
The world of manufacturing, particularly in the automotive sector, constantly demands innovations that enhance efficiency and durability. One such innovation that has paved the way for better corrosion resistance and paint adhesion is the phosphating plant. In this article, we delve into the significance of phosphating plants, their operational mechanisms, benefits, and the future of this technology in the automotive and paint industry.
The Process of Phosphating
Phosphating is a chemical treatment process that involves the conversion of the surface of metals into a protective phosphate coating. This process is essential in enhancing corrosion resistance, improving paint adhesion, and increasing the overall lifespan of automotive components. The typical steps involved in the phosphating process include:
- Cleansing: The metal surface is thoroughly cleaned to remove any dirt, oil, or grease. This step is crucial for the effectiveness of the phosphating treatment.
- Activation: The cleaned metal is often treated with an acid solution to activate the surface and promote better adhesion of the phosphate coating.
- Phosphating: The metal is then immersed in a phosphating solution that contains phosphoric acid and other chemicals. Here, the magic happens as a crystal structure forms on the metal surface.
- Rinsing: After the phosphating treatment, the parts are rinsed to remove any residual chemicals, leaving a clean and well-coated surface.
- Dried and Coated: Finally, the parts are dried and can be painted or coated as needed, taking full advantage of the improved surface properties provided by the phosphating process.
Advantages of Using Phosphating Plants
Phosphating plants deliver several significant benefits, particularly in the automotive and paint sectors:
1. Enhanced Corrosion Resistance
Phosphating creates a robust barrier on metal surfaces, significantly improving their resistance to corrosion. This is particularly important in automotive applications, where components are frequently exposed to moisture and varying weather conditions.
2. Improved Paint Adhesion
The phosphate coating provides an excellent surface for paint applications. It promotes better adhesion, ensuring that the paint bonds effectively to the metal surface, which is vital for aesthetic and protective purposes.
3. Increased Durability of Coatings
Vehicles and machinery that undergo phosphating treatment tend to have more durable coatings that can withstand harsh environmental conditions, thus prolonging their lifespan.
4. Cost-Effectiveness
Implementing a phosphating plant may seem like a significant upfront investment, but the improved product durability and reduced maintenance needs result in long-term cost savings.
5. Eco-friendly Options
Modern advancements in phosphating technology have led to eco-friendly processes that minimize hazardous waste while still delivering quality results. These options align with the industry's growing emphasis on sustainable practices.
Key Components of a Phosphating Plant
To fully appreciate the functionality of a phosphating plant, it is essential to understand its key components:
1. Pre-treatment Tanks
These tanks are designed for the cleansing and activation of metal parts. Proper pre-treatment is crucial for the success of the phosphating process.
2. Phosphating Tanks
The core of the facility, these tanks hold the phosphating solution and are equipped with precise temperature controls and chemical management systems.
3. Rinsing Stations
After phosphating, metal parts require thorough rinsing to eliminate excess solutions, ensuring a clean finish.
4. Drying Ovens
These ovens effectively dry the components and are critical to preventing moisture-related issues before the application of paint or other coatings.
5. Quality Control Stations
Incorporating quality control measures ensures that all finished products meet industry standards and client expectations.
Innovations in Phosphating Technology
The landscape of phosphating technology continually evolves with research and innovation. Some notable advancements include:
1. Replacement of Traditional Phosphating Processes
Recent innovations have introduced alternative methods such as non-phosphorus and zirconium-based coatings that offer similar benefits with reduced environmental impact.
2. Automation and Robotics
Integrating automation in phosphating plants enhances operational efficiency and reduces labor costs while ensuring consistent quality in finishing processes.
3. Real-time Monitoring Systems
Modern phosphating plants are increasingly implementing IoT solutions for real-time monitoring of chemical concentrations and process parameters, improving overall control and efficiency.
Challenges Facing Phosphating Plants
Despite their benefits, phosphating plants face several challenges that operators must navigate:
1. Environmental Regulations
With increasing environmental awareness, phosphating plants must comply with stricter regulations, necessitating investments in waste treatment and management systems.
2. Material Compatibility
Phosphating treatments must be carefully selected based on the materials being treated, as some substrates may react differently to phosphating solutions.
3. Rising Costs of Raw Materials
The fluctuating prices of the chemicals used in the phosphating process can impact production costs and require effective supply chain management.
Conclusion: The Future of Phosphating Plants in the Automotive Industry
As the automotive industry continues to prioritize sustainability and efficiency, the role of phosphating plants remains pivotal. By adopting modern technologies and practices, these facilities will not only enhance the performance and longevity of automotive components but also contribute to a greener manufacturing landscape.
In conclusion, the phosphating plant is more than just a processing unit; it is a cornerstone of automotive manufacturing that supports durability and quality. As advancements continue to arise, those involved in the automotive industry must stay informed about phosphating technologies to maintain competitive advantage.